Principle and technology of cold rolling pickling
Release time:
2023-06-14
Iron oxide is the chemical interaction between iron and oxygen or the product of iron and fuel combustion (CO2, H2O, etc.) during the rolling process of the rolling mill, and an oxide layer is formed, which is called oxide.
Iron oxide is the chemical interaction between iron and oxygen or the product of iron and fuel combustion (CO2, H2O, etc.) during the rolling process of the rolling mill, and an oxide layer is formed, which is called oxide.
Due to the composition of the metal, surface temperature, heating and cooling system, the oxygen content of the surrounding medium and other factors, the composition and structure of the oxide sheet also vary. Generally speaking, the more active the chemical properties of the metal, the higher the temperature, the faster the oxidation rate of the metal. The longer the oxidation time, the greater the thickness of the oxide sheet. The oxide and structure of iron are also relatively loose, and the rolling of steel and the processing of iron products are mostly carried out at a higher temperature, therefore, the oxidation rate of steel is accelerated, and the formation of iron oxide sheet on the steel surface is promoted. Because of the different chemical composition, rolling temperature, cooling rate and coiling temperature of hot rolled strip, the structure, thickness and properties of the oxide sheet formed on the surface of the strip are also different.
Three layers are distributed on the surface of the heated billet:
· The innermost layer is composed of FeO of fine particles, accounting for 40% of the total thickness of the oxide layer;
· The middle layer is composed of Fe3O4 of coarse particles, accounting for about 50% of its thickness;
· The outermost layer is composed of Fe2O3, accounting for about 10%.
Due to the inconsistent expansion coefficient of the iron oxide and steel, the quality is brittle, there is no extensibility, it is loose and easy to fall off under mechanical action and hot processing, and the melting point of the iron oxide (1300 ~ 1350℃) is low, resulting in steel heating at high temperature, the falling off or melting of the iron oxide will expose the surface of the metal, when the electrolyte pouring into the crack, Iron and oxide form a primary cell. The oxide is the cathode, and the iron as the anode accelerates the corrosion, so the larger the area of the oxide, the oxidation continues to accelerate, the faster the corrosion rate of the steel matrix, the more serious the corrosion.
Related News
Public account
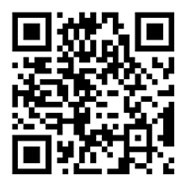
ZhongAn (Qian'an) Steel Plate
Add: No. 6899 Qiguang Street, High-tech Industrial Development Zone, Qian 'an City, Hebei Province
Tel: +86-0315-5671599 / 5671699
Fax: +86-0315-5671799
Copyright © 2023 ZhongAn (Qian'an) Steel Plate Manufacturing Co., Ltd.